12 Tips to Improve Productivity at a Manufacturing Company
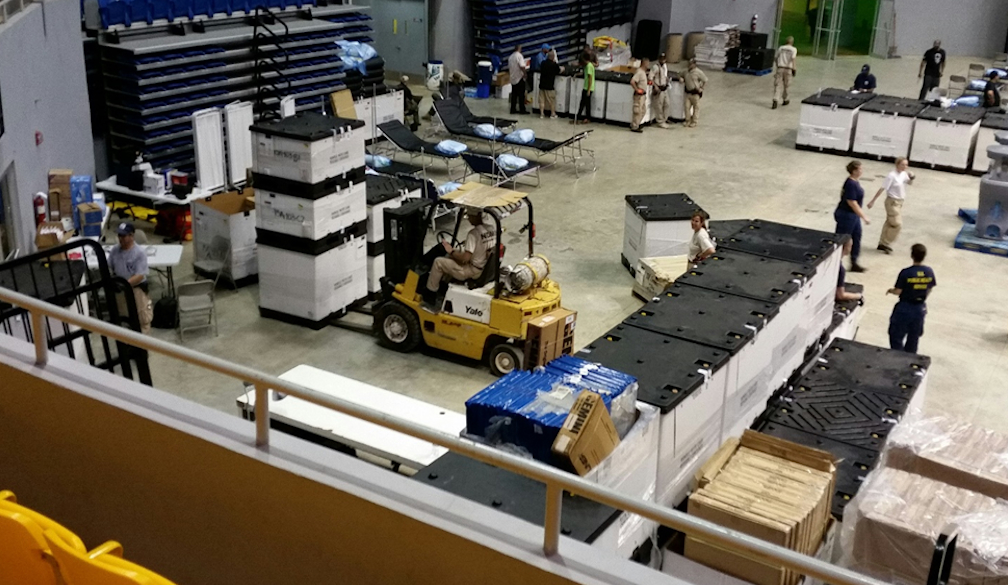
Whether it's about optimizing production lines, reducing downtime, or enhancing the quality of outputs, every aspect plays a crucial role in the overall efficiency of a manufacturing company. However, improving productivity is often easier said than done. It requires a strategic approach, encompassing everything from employee engagement to technological advancements. In this article, we will discuss practical tips that can help manufacturing companies boost their productivity.
- Streamlining Workflow Processes
The first step towards boosting productivity is streamlining workflow processes. This involves a thorough analysis of current operations to identify bottlenecks and inefficiencies. Implementing lean manufacturing principles can significantly help in eliminating waste and reducing unnecessary steps in the production process. Workflow mapping, another effective tool, allows for a visual representation of every step in the manufacturing process, making it easier to spot areas for improvement. Streamlining speeds up the production and improves the quality of the end product, leading to increased customer satisfaction.
- Investing in Employee Training and Development
Employees are the backbone of any manufacturing company. Investing in their training and development is essential for enhancing productivity. Regular training programs keep the workforce up-to-date with the latest industry practices and technologies. Skill development initiatives empower employees to handle a wider range of tasks more efficiently. This not only boosts their morale but also makes the workforce more versatile and adaptable to changing production demands. A well-trained team is more capable of handling challenges and contributing effectively to the company's goals.
- Efficient Packaging Solutions
Efficient packaging solutions play a significant role in improving productivity in manufacturing. Packaging for manufacturing companies should be designed to protect the product, while also being cost-effective and time-efficient. Opting for custom packaging solutions that fit the product perfectly can reduce material waste and packing time. Additionally, using sustainable and lightweight materials can lower shipping costs and benefit the environment.
- Implementing Automation and Technology
The adoption of automation and advanced technology is a game-changer in manufacturing. Automation of repetitive tasks can significantly reduce manual errors and increase the speed of production. Technologies like AI and IoT (Internet of Things) can also be integrated to monitor machine performance and predict maintenance needs, minimizing downtime. Investing in state-of-the-art machinery and software might require upfront costs, but the long-term gains in productivity are well worth it. Embracing technology keeps a company at the forefront of innovation and competitive in the market.
- Regular Maintenance of Equipment
Regular and preventive maintenance of equipment is essential to avoid unexpected breakdowns and production halts. A well-maintained machine functions efficiently and has a longer lifespan. Establishing a routine maintenance schedule ensures that equipment is always in optimal working condition. This includes regular inspections, timely repairs, and replacements of worn-out parts. Proactive maintenance can significantly reduce the risk of costly downtime and keep the production line running smoothly.
- Quality Control Measures
Poor quality products result in rework and waste, which are detrimental to efficiency. Setting up a reliable quality control system ensures that the products meet or exceed the set standards, reducing the likelihood of defects. This involves regular monitoring at every stage of the production process, from raw material procurement to the final output. Investing in quality control improves productivity and also builds a reputation for reliability and excellence in the market.
- Effective Inventory Management
Efficient inventory management is pivotal in maintaining a smooth production flow. Excessive inventory can lead to increased costs and storage issues, while too little can cause delays and lost sales opportunities. Adopting inventory management techniques like Just-In-Time (JIT) can help in keeping inventory levels balanced – ensuring that materials are available when needed but not overstocked. This approach reduces waste and storage costs while improving cash flow. Using inventory management software can provide real-time tracking and better control over stock levels.
- Clear Communication Channels
Clear and effective communication is vital in a manufacturing environment. It ensures that everyone is on the same page, from the shop floor to upper management. Establishing open communication channels helps in quickly addressing issues, sharing important updates, and facilitating collaborative problem-solving. This can be achieved through regular team meetings, digital communication tools, and ensuring that all employees have access to necessary information.
- Employee Involvement and Feedback
Encouraging employee involvement and seeking their feedback can lead to significant improvements in productivity. Employees who are directly involved in the production process often have valuable insights into how to address problem areas. Creating a platform where they can voice their suggestions and feedback fosters a sense of ownership and engagement. Implementing their viable ideas improves processes and boosts morale and job satisfaction, leading to increased productivity.
- Fostering a Positive Work Environment
A positive work environment is key to employee performance and productivity. A supportive atmosphere that values employee well-being and offers opportunities for growth and recognition can significantly boost morale. This includes ensuring a safe work environment, offering fair compensation, and recognizing and rewarding good performance. A happy and motivated workforce is more likely to be productive and committed to the company’s success.
- Setting Realistic Goals and Objectives
Setting clear, realistic goals and objectives is essential for driving productivity. These goals provide direction and a sense of purpose, helping teams to focus their efforts on what matters most. It’s important to ensure that these goals are achievable and aligned with the overall company strategy. Regularly reviewing and adjusting these goals based on performance and market changes can also help in maintaining relevance and motivation.
- Analyzing and Adapting to Market Trends
In a rapidly changing manufacturing landscape, staying adaptable and responsive to market trends is important. This involves keeping up to date on industry developments, emerging technologies, and changing consumer demands. Being able to quickly adapt production processes, product lines, or business strategies in response to these trends can give a company a competitive edge. Continuous market analysis and a willingness to innovate are key to staying relevant and productive in a dynamic market.
In summary, improving productivity in a manufacturing company requires attention to various aspects of the operation. From optimizing workflows and investing in technology to fostering a positive workplace and adapting to market trends, each element plays an essential role. By implementing these strategies, manufacturing companies can improve their efficiency and position themselves for long-term success in a competitive industry.