Maximising Warehouse Space with Efficient Pallet Racks
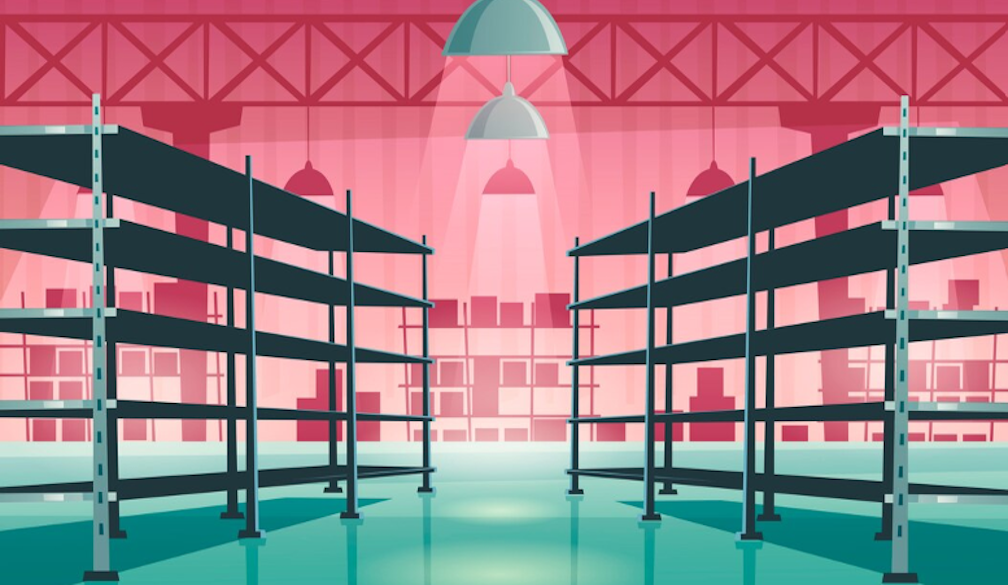
Pallet racking systems are vital in managing warehouses or in making a particular warehouse meet its organisational purpose or goal. From an enormous distribution terminal to a petty warehouse, choosing the proper pallet racking system substantially influences the operation's performance, safety, and profitability.
This blog will look at how pallet racking complements warehouse storage, the benefits of pallet racking structures, factors to consider while choosing a pallet racking system, and a way to pick the appropriate pallets for your organisation.
Learning About Pallet Racking Systems
Pallet racking systems are industrial storage systems that utilise upright space optimally. These structures are available in various configurations to complement multiple consumer demands, such as:
- Selective Pallet Racking: It is the most common kind because it gives a short and smooth right of entry to individual pallets.
- Drive-In Pallet Racking: This system designs a deep pallet space inside the rack, supplying high storage density.
- Push-Back Pallet Racking: This pallet system uses gravity to push loaded pallets again toward the rear, freeing space for brand-new ones and expanding the storage area.
- Cantilever racking: This type of racking is perfect for holding oversized, prolonged items like wood or pipes.
Advantages of Using a Pallet Racking System
- Increased Storage Capacity: Pallet racking systems significantly amplify the amount of storage space that can be saved in a specific warehouse location by taking advantage of vertical space.
- Increased Order Picking Efficiency: Emphasised and systematically stored pallet racking systems ensure faster and more efficient order-picking steps.
- Improved Inventory Control: The visibility of stored items reduces the risks of stockouts or overstocking as it is easy to manage stored items.
- Improved Safety: Pallet racking systems are safe when properly installed and adequately maintained following specific standards.
- Cost Savings: Organisational and effective utilisation of space and time reduces pallet racking costs.
Considerations on Selecting Pallet Racking
- Warehouse Layout:
Review the dimensions, ceiling heights, and column positions in your warehouse. The pallets chosen should enhance the layout of the building where the storeroom's racking will be located, as should the design of the racking system itself.
- Weight and Volume of Goods
The type and weight of storage must be considered to avoid product spoilage and deficiency. Fourth, specialised racks must be placed for cumbersome products, while light racks are enough for small products.
- Accessibility Requirements
Determine the rate at which inventory has to be retrieved in the organisation. Selective pallet racking is suitable for high accessibility, and drive-in racks are meant for storage with minimal turnovers.
- Budget and Investment
There are low, mid, and high-priced pallet racking systems. However, several systems that cost significantly more in the initial stages may yield good returns in the long run due to an efficiency boost. Coordinate your budget with your operations.
- Safety Standards
Check whether the racking system complies with essential requirements, such as the firm's maximum allowable load per pallet or any other load-bearing aspect. Adopt proper inspection and maintenance measures to reduce the threat of complaints.
Best Practices for Choosing Pallet Racking System
Using efficient management and storage techniques is crucial to optimising the advantages of pallet racking systems. Consider the following best practices:
1) Appropriate Pallet Loading
- Even Weight Distribution: To avoid tipping and structural damage to the racking system, ensure the pallet's weight is dispersed equally throughout.
- Secure Load: Using the proper wrapping or strapping techniques to keep the load from moving while being transported or stored.
- Respect for Pallet Dimensions: Use pallets of the same size and quality to preserve uniformity and maximise storage space.
- Avoid Overloading: It becomes dangerous to overload pallets, and the racking system may be destroyed.
2) Choose Proper Storage Height and Accessing Point
- Consider Forklift Capabilities: This racking system's height should conform with the reach of your forklifts.
- Optimise Storage Density: Ensure enough space for storage while maximising efficiency when it comes to order picking.
- Utilise Mezzanine Floors: If needed, it is recommended that mezzanine floors be constructed for additional storage space.
3) Explicit Labelling and Inventory Control
- Clear and Consistent Labelling: Label pallets, racking positions, and aisles clearly and consistently.
- Accuracy can be increased, and inventory tracking can be computerised using barcodes and RFID technology.
- Frequent Inventory Audits: To reconcile stock information and discover inconsistencies, carry out recurring physical stock counts.
- The precept of First-In, First-Out (FIFO): Use older stock by adhering to the FIFO precept, lowering the danger of inventory obsolescence or spoiling.
4) Effective Warehouse Layout
- Optimise Workflow: Organise the warehouse's space flow so workers travel as little as possible to complete all jobs.
- Consider Aisle Widths: After careful observation of forklift activities, it is recommended that aisles have adequate width to allow forklift passage and provide convenient access to pallets.
- Utilise Zoning: Subdivide the warehouse into zones for adequate product storage and access and various processes.
- Flexible Design: Any decision on the layout should be made with an eye on future growth and storage requirements' flexibility.
Thus, through their implementation and maintenance, effective pallet racking systems will help companies achieve better results in warehouse operations and provide a competitive advantage.