Opportunities and Challenges for Australia's Manufacturing Sector in 2025
- Written by Rob Cheesman, General Manager – Business Applications, Atturra
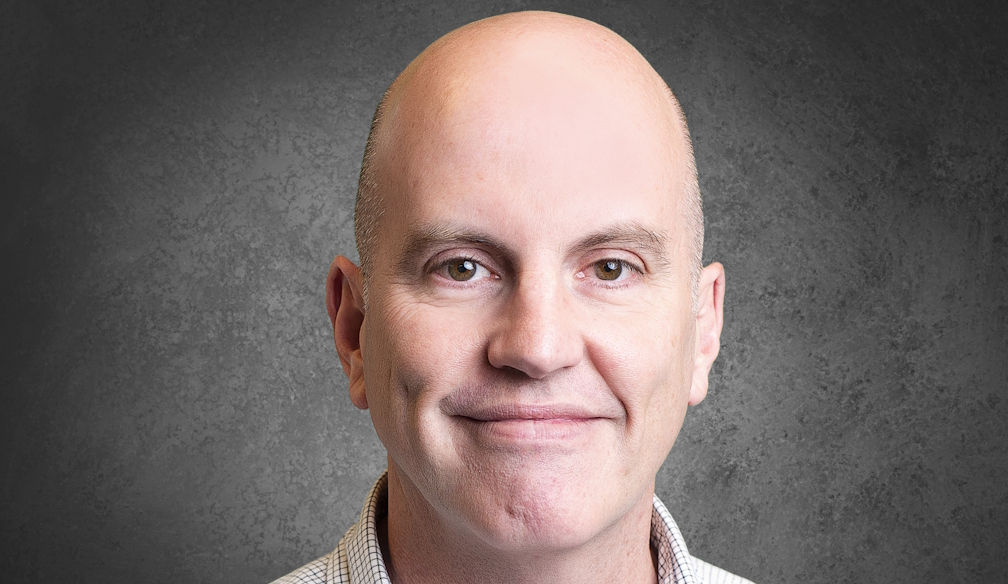
As the new year begins to unfold, Australia’s manufacturing sector is bracing for a transformative period shaped by technological advancements and evolving workforce dynamics.
Despite the associated challenges, the sector offers significant growth opportunities for those companies ready to adapt. Navigating these transitions, however, will demand agility, innovation, and a focus on resilience.
Supply chain reliability
In recent years, the reliability of global supply chains has been severely tested. Natural disasters, geopolitical tensions, and industrial disputes have all contributed to disruptions, highlighting the fragility of existing systems.
To counteract these challenges, businesses are increasingly turning to local suppliers and investing in technologies that improve supply chain visibility. Predictive analytics, for example, allows companies to anticipate disruptions and make proactive adjustments.
Meanwhile, digital platforms that facilitate real-time communication with suppliers and logistics providers are becoming essential tools for maintaining operational continuity. By diversifying supply sources and building flexible logistics networks, manufacturers can enhance their resilience against future shocks.
Workforce transformation and engagement
The factory floor is undergoing a transformation as connected systems and automation redefine traditional roles. Automation is often implemented as a response to workforce shortages but by automating a job, it becomes less rewarding, often making the engagement problem worse.
Connected Workforce solutions (e.g. QAD Redzone) are fostering leaner processes and improving staff engagement, with tangible benefits for both morale and productivity. Working in manufacturing is and should be rewarding, and systems like this make coming to work so much more attractive.
Tools that empower workers - such as augmented reality (AR) devices for training or intuitive shopfloor dashboards - are proving their worth in creating more effective teams. However, technology alone cannot guarantee success.
Workforce engagement strategies that prioritise communication, recognition and skill development are also critical. As automation takes over routine tasks, upskilling workers to operate and maintain advanced systems becomes a top priority.
Energy cost and reliability
In recent years, the cost and reliability of energy has had an enormous impact on manufacturing companies. Often costs are direct and obvious, in the form of electricity and gas. With indirect costs like transport and raw materials having an impact.
Manufacturers have always been focused on efficiency so these higher costs are hard to avoid but a relentless approach to removing waste throughout the supply chain must continue. When energy is unreliable, what is an inconvenience for many of us, can actually shut a manufacturer down.
In the US, major IT companies such as Google and Microsoft are investing in nuclear. While obviously out of reach for local manufacturers, companies are being forced to look at options they wouldn’t normally such as generators and standby power.
The rise of additive manufacturing
Additive manufacturing, commonly known as 3D printing, has been hailed as a game-changer for the sector. This technology enables rapid prototyping, customisation, and on-demand production, offering solutions to some of the industry's most persistent challenges, such as long lead times and material waste.
While the initial uptake has been slow due to cost and reliability concerns, recent advancements have addressed many of these barriers. Affordable, user-friendly 3D printing solutions are now entering the market, opening up new possibilities for small and medium enterprises (SMEs) as well as large manufacturers.
Global trade and geopolitical disruptions
The global trade landscape is becoming increasingly uncertain, with policies such as proposed US import tariffs under the Trump administration creating ripple effects worldwide. For Australian manufacturers, this uncertainty underscores the importance of diversifying export markets and strengthening trade ties, particularly within the Asia-Pacific and Europe.
In addition to trade policies, manufacturers must contend with evolving consumer preferences driven by globalisation and e-commerce. Direct-to-consumer (DTC) models are bypassing traditional retail channels, forcing manufacturers to rethink their distribution strategies. Companies that can adapt to these changes by offering personalised, high-quality products and streamlined delivery options will have a competitive edge.
IIoT gaining traction
The Industrial Internet of Things (IIoT) has been a buzzword for years, but its practical applications are now coming to fruition. Advances in sensor technology and analytics software are driving down costs, making IIoT solutions more accessible than ever.
These devices provide real-time data on production processes, equipment performance, and supply chain operations, enabling manufacturers to make informed decisions quickly.
For example, sensors at the start and end of a production line can provide insights into bottlenecks, ensuring consistent quality and reducing downtime. Meanwhile, IIoT-enabled machinery can predict maintenance needs, preventing costly breakdowns.
Strengthening cybersecurity defences
As manufacturing becomes increasingly digitised, cybersecurity has emerged as a critical concern. Hackers are employing sophisticated tactics, including ransomware attacks, to target vulnerable systems. The consequences of a successful breach can be devastating, ranging from stolen intellectual property to prolonged operational downtime.
To address these risks, manufacturers must adopt a multi-layered cybersecurity approach. This includes investing in robust firewalls and encryption, conducting regular vulnerability assessments, and training employees on best practices. Moreover, as regulatory frameworks evolve to address cybersecurity threats, compliance will become an essential part of doing business.
Sustainability becoming a competitive advantage
Consumers, investors, and regulators alike are demanding greater accountability from manufacturers regarding their environmental impact. This shift presents both challenges and opportunities.
On one hand, meeting stricter environmental standards may require significant investment in cleaner technologies and processes. On the other, adopting sustainable practices can open new markets and enhance brand reputation.
From reducing energy consumption to incorporating recycled materials into products, manufacturers that lead on sustainability will be well-positioned to succeed in a green-conscious economy.
Embracing the Future with Caution and Confidence
During 2025, Australia’s manufacturing sector will find itself at a crossroads. While the challenges are undeniable - supply chain disruptions, workforce engagement, energy costs, and global trade uncertainties - the opportunities are equally compelling.
Ultimately, the manufacturers that embrace change, invest in their workforce, and prioritise resilience will be the ones shaping the industry’s future. By balancing caution with confidence, the manufacturing sector can emerge stronger, more innovative, and better prepared for the challenges of the decade ahead.