Protecting What Matters: The Business Case for Bunding
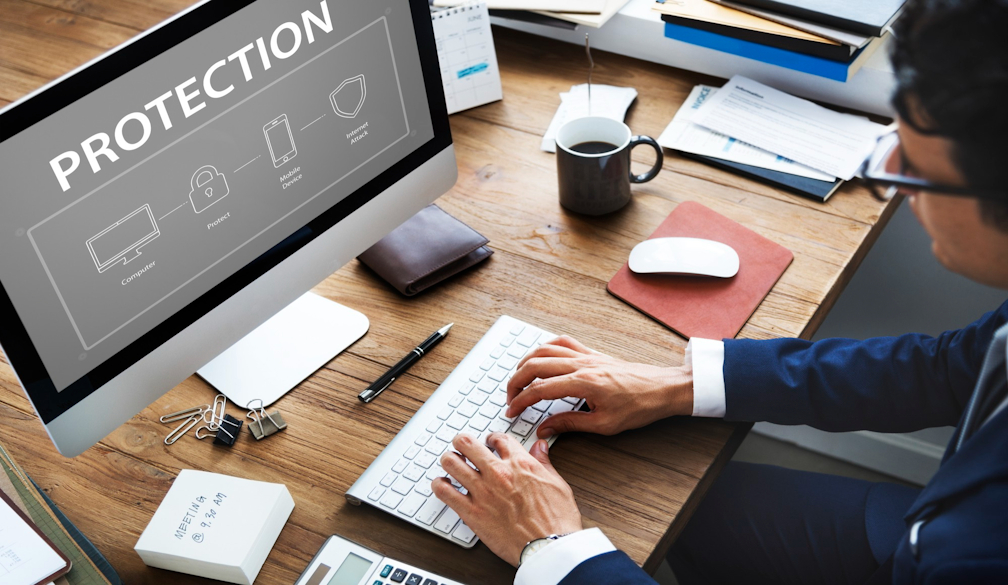
A responsible business doesn't just plan for success it plans to protect everything and everyone that makes that success possible.
Written for warehouse & facility managers, safety & compliance officers, and business owners in logistics, manufacturing, and warehousing industries.
The Hidden Risks in Your Facility
In today's complex operational environments, facility managers and safety officers face an array of challenges. While many focus their attention on obvious safety concerns like trip hazards, machinery guarding, and fire prevention, some of the most significant threats remain largely invisible until disaster strikes.
Liquid spills particularly those involving hazardous chemicals, fuels, oils, and other controlled substances represent one of these hidden threats. A single container failure, damaged valve, or accidental puncture can release substances that threaten worker safety, damage expensive equipment, contaminate inventory, and potentially cause environmental damage that extends far beyond your facility's boundaries.
What makes these risks particularly concerning is their potential for rapid escalation. A seemingly minor leak can quickly become a major incident if the released substance can flow freely across your facility floor, enter drainage systems, or reach groundwater. This is where proper containment planning becomes not just advisable, but essential.
The Real Cost of Containment Failures
For business owners and facility managers, understanding the potential financial impact of containment failures provides important context for investment decisions. Consider these sobering statistics:
- The average cost of environmental cleanup for a significant chemical spill exceeds $100,000
- Regulatory penalties for preventable spills commonly range from $10,000 to $50,000 per incident
- Operational downtime during cleanup can cost manufacturers thousands of dollars per hour
- The average workers' compensation claim for chemical exposure or injury exceeds $20,000
These direct costs don't account for potential long-term consequences like increased insurance premiums, damaged business relationships, and reputational harm that can persist long after the immediate incident is resolved.
Safety officers and compliance managers understand that preventable incidents don't just impact the bottom line—they can affect careers. Facilities with repeated containment failures often face increased regulatory scrutiny, making compliance increasingly difficult and time-consuming.
Bunding: Your First Line of Defense
This is where bunding enters the conversation. At its core, bunding is simply a secondary containment system designed to catch and contain spills from primary containers before they can spread throughout your facility or into the environment.
The principle is straightforward: create a barrier or reservoir that can capture and hold the contents of your storage containers if they leak or fail. While the concept is simple, effective implementation requires careful planning and consideration of your specific operational needs.
Bunding Basics: What Every Facility Manager Should Know
The golden rule in bunding design is that your containment system should be able to hold at least 110% of the volume of your largest storage container or 25% of the total stored volume, whichever is greater. This ensures that even a catastrophic failure of your largest container can be fully contained.
Different industries and jurisdictions may have specific regulatory requirements that exceed these minimums, particularly for highly hazardous substances. As a compliance officer, staying informed about these requirements is essential for avoiding costly violations.
Types of Bunding Solutions
Modern bunding solutions come in various forms to address different operational needs:
Permanent Concrete Bunds: These built-in solutions are commonly found around large tank farms and fixed storage areas. They offer exceptional durability and can be designed to contain large volumes, but they represent a significant initial investment and lack flexibility for changing operational needs.
Modular Containment Systems: These prefabricated units can be arranged to create custom containment areas. Available in both plastic and metal varieties, they offer a balance of durability and flexibility that makes them ideal for warehousing operations where storage arrangements may change periodically.
Spill Pallets and Containment Decks: Perfect for drum storage and other smaller containers, these raised platforms include integrated sumps that capture drips and spills. They allow for easy inspection and typically include forklift access points for simplified material handling.
Flexible Bunding: These portable, often foldable barriers can be deployed quickly to create temporary containment areas. They're ideal for maintenance operations, temporary storage situations, or creating emergency containment during incidents.
IBC Bunds: Specifically designed for Intermediate Bulk Containers, these units accommodate the unique footprint and volume of IBCs while providing adequate containment capacity.
Sump Trays and Drip Containment: For machinery with hydraulic systems, fuel tanks, or other potential leak points, these low-profile containment solutions capture small leaks before they can spread.
For warehouse managers concerned with space utilization, many modern bunding solutions are designed with efficiency in mind. Stackable designs, integrated storage features, and space-saving configurations help balance safety requirements with practical operational needs.
Beyond Compliance: The Strategic Value of Proper Bunding
While regulatory compliance often drives initial bunding implementations, forward-thinking business owners and facility managers recognize that effective containment delivers benefits far beyond avoiding penalties:
Operational Continuity: By preventing small leaks from becoming major incidents, proper bunding helps maintain productive operations without unexpected shutdowns.
Asset Protection: Secondary containment protects valuable equipment, inventory, and infrastructure from damage caused by corrosive or contaminating substances.
Insurance Advantages: Many insurers offer preferred rates to facilities with comprehensive spill containment systems, recognizing the reduced risk profile these measures create.
Environmental Stewardship: Preventing contaminants from reaching soil, waterways, and groundwater demonstrates environmental responsibility that resonates with customers, partners, and community stakeholders.
Employee Confidence: Workers who see tangible safety measures in place develop greater confidence in management's commitment to their wellbeing often translating to improved morale and retention.
For safety officers looking to build organizational buy-in for containment investments, emphasizing these broader benefits can help shift the conversation from mere compliance to strategic risk management.
Implementation: From Assessment to Action
Implementing effective bunding solutions begins with a comprehensive assessment of your facility's unique needs. Consider these key steps:
- Conduct a thorough inventory of all stored liquids, noting volumes, container types, locations, and hazard classifications.
- Identify vulnerable areas where spills would cause the most significant damage or where containment is currently inadequate.
- Assess traffic patterns and operational workflows to ensure bunding solutions won't impede necessary movement or create new hazards.
- Consider substance compatibility when planning containment. Some chemicals require specialized containment materials to prevent degradation or dangerous reactions.
- Develop a maintenance schedule for both primary containers and secondary containment systems. Regular inspection prevents degradation that could compromise effectiveness.
- Train staff on the purpose and proper use of bunding systems. Even the best-designed containment solutions can be compromised by improper use or unauthorized modifications.
For logistics operations and warehouses where storage arrangements change frequently, implementing a combination of fixed and flexible bunding solutions often provides the optimal balance of protection and adaptability.
Maintenance: Ensuring Ongoing Protection
Like any safety system, bunding requires regular attention to maintain its effectiveness. Facility managers should establish routine inspection protocols that include:
- Checking for cracks, corrosion, or other damage to containment surfaces
- Ensuring drains and valves are functioning properly and secured in the closed position
- Removing accumulated rainwater from outdoor bunding (following proper testing and disposal procedures)
- Verifying that bunding is free from debris that could reduce effective containment volume
- Confirming that warning signs and labels remain visible and legible
For compliance officers, maintaining detailed records of these inspections provides valuable documentation for regulatory reviews and can help demonstrate due diligence in the event of an incident.
Protection as an Investment, Not an Expense
For business owners, warehouse managers, and safety officers, implementing proper bunding represents an investment in operational resilience and risk mitigation. Rather than viewing containment systems as simply a regulatory requirement, recognizing their role in protecting people, property, and the environment helps justify the allocation of resources to these critical systems.
The question isn't whether your facility can afford proper bunding it's whether you can afford the potential consequences of inadequate containment. By taking proactive steps today to assess your needs and implement appropriate solutions, you create a safer, more sustainable operation that's better positioned to thrive in an increasingly regulated environment.
Remember that effective bunding isn't just about having the right equipment—it's about fostering a culture where spill prevention and containment are recognized as fundamental aspects of responsible operations. When leadership demonstrates this commitment through tangible investments in appropriate containment systems, the entire organization benefits from enhanced safety, improved compliance, and greater peace of mind.
For facility managers and safety officers looking to make a meaningful impact on their organization's risk profile, few initiatives offer the combination of regulatory compliance, operational protection, and environmental responsibility that proper bunding provides.