Precision in Every Turn: Examining High-Speed Coil-Winding Machines
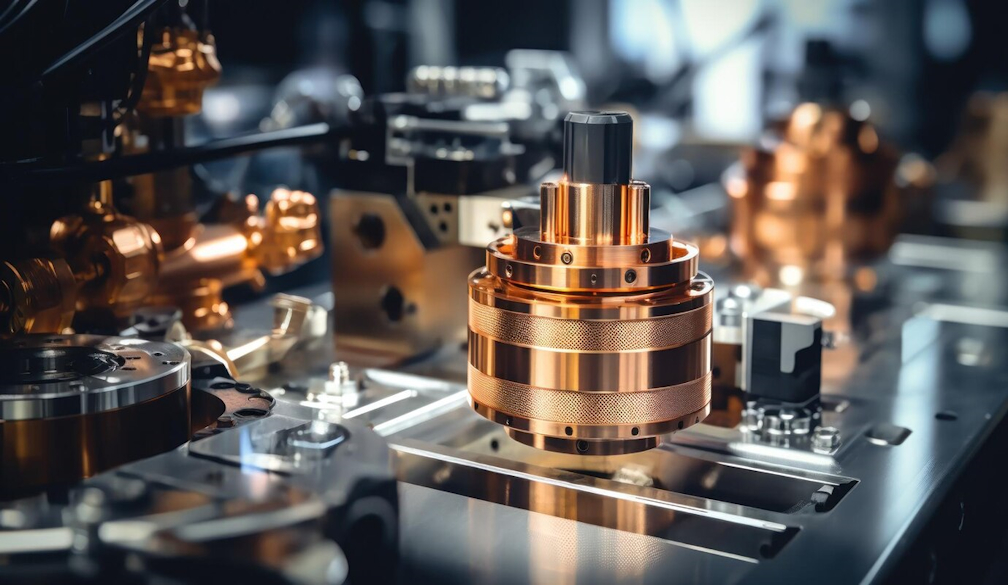
In the world of manufacturing, especially within industries like electronics, automotive, and renewable energy, the demand for efficient and precise coil winding processes has grown significantly. This demand has propelled the development of high-speed coil-winding machines, which play a crucial role in creating coils used in electric motors, transformers, generators, and various other electromechanical devices. In this blog, we delve into the intricacies of these advanced machines, exploring how they achieve precision in every winding coil.
Understanding Coil Winding
Before diving into the technology behind high-speed coil-winding machines, it's essential to grasp the fundamental concept of coil winding. Coil winding involves the process of winding wire or another conductor material onto a form, spool, or core to create electromagnetic components. The resulting coils can serve different purposes, such as conducting electricity, inducing magnetic fields, or transforming electrical energy.
The key challenge in coil winding lies in achieving uniformity, precise turns, and desired electrical properties. Traditional methods, though effective, often lack the efficiency required for modern manufacturing demands. This gap has spurred the development of high-speed coil-winding machines.
The Role of High-Speed Coil-Winding Machines
High-speed coil-winding machines are engineered to meet the demand for rapid, accurate, and consistent coil production. These machines leverage advanced automation, computer controls, and specialized winding techniques to enhance productivity and quality. Let's explore the key features and technologies that enable these machines to achieve exceptional performance:
Precision Engineering
High-speed coil winders are engineered with precision in mind. They utilize advanced servo motors and motion control systems to ensure precise positioning and tension control during winding. This level of precision is crucial for maintaining uniform wire tension and achieving consistent coil dimensions.
Automated Control Systems
Modern coil winders are equipped with sophisticated control systems that automate the winding process. Operators can program parameters such as wire diameter, number of turns, winding pattern, and tension settings. This automation not only enhances productivity but also minimizes human error, leading to higher-quality coils.
Multi-Axis Winding Heads
Many high-speed coil-winding machines feature multi-axis winding heads that can move in multiple directions simultaneously. This capability allows for complex coil designs and precise wire layering, allowing manufacturers to produce intricate coil configurations with exceptional accuracy.
Tension Management
Maintaining consistent tension throughout the winding process is critical for producing high-quality coils. Advanced coil winders employ intelligent tension control mechanisms that adjust automatically based on winding parameters and wire characteristics. This ensures that the wire is wound evenly without stretching or breaking.
Real-Time Quality Monitoring
High-speed coil winders are often equipped with real-time monitoring systems to meet stringent quality standards. These systems use sensors to detect variations in winding tension, wire diameter, and other parameters. Operators can promptly identify and address issues, minimizing defects and waste.
Material Compatibility
High-speed coil-winding machines are designed to handle a wide range of conductor materials, including copper, aluminum, and various alloys. They can accommodate different wire gauges and insulation types, ensuring flexibility in coil production.
Speed and Efficiency
The primary advantage of high-speed coil winders is their ability to significantly reduce cycle times compared to manual or slower automated methods. This increased efficiency translates into higher production output and lower manufacturing costs.
Customization and Flexibility
Modern coil-winding machines offer customizable features to meet specific customer requirements. Operators can easily adjust parameters such as coil diameter, pitch, and layering to produce coils tailored to unique applications.
Quality Assurance
Quality control is paramount in coil production. High-speed winding machines are equipped with built-in checks and balances to ensure each coil meets strict quality standards. This includes verifying wire tension, insulation integrity, and dimensional accuracy throughout the winding process.
Environmental Considerations
Efforts are underway to develop eco-friendly practices in coil winding, such as using recycled materials and optimizing energy consumption. High-speed coil-winding machines are evolving to align with sustainable manufacturing practices, reducing waste and environmental impact.
Applications of High-Speed Coil-Winding Machines
The versatility of high-speed coil-winding machines makes them indispensable across various industries:
- Automotive: Electric vehicles rely on high-performance motors with precision-wound coils for optimal efficiency and power delivery.
- Consumer Electronics: Devices such as loudspeakers, actuators, and sensors require custom coils that can be efficiently produced using advanced winding machines.
- Renewable Energy: Wind turbines, solar inverters, and other renewable energy systems utilize coils wound with high-speed precision for maximum energy conversion.
- Industrial Automation: Coil-winding machines play a vital role in producing industrial machinery and equipment, ensuring the reliable operation of motors, solenoids, and transformers.
Challenges and Future Trends
Despite their advanced capabilities, high-speed coil winders face ongoing challenges, such as handling ultra-fine wires, optimizing cycle times, and integrating with Industry 4.0 technologies. Future trends are likely to focus on:
- Smart Manufacturing: Integration with IoT (Internet of Things) devices for predictive maintenance and real-time performance optimization.
- Material Innovations: Developing new conductor materials to enhance efficiency and reduce environmental impact.
- Advanced Robotics: Incorporation of robotic arms for complex winding tasks and flexible production setups.
Conclusion
High-speed coil-winding machines represent a cornerstone of modern manufacturing, enabling the efficient production of high-quality coils essential for numerous applications. These machines empower industries to meet growing demands for sophisticated electromagnetic components by harnessing precision engineering, automation, and advanced control systems. As technology continues to evolve, we can expect further innovations that push the boundaries of coil-winding efficiency and performance.