Keeping Your Machines Running Smoothly: The Importance of Hydraulic Cylinder Repair
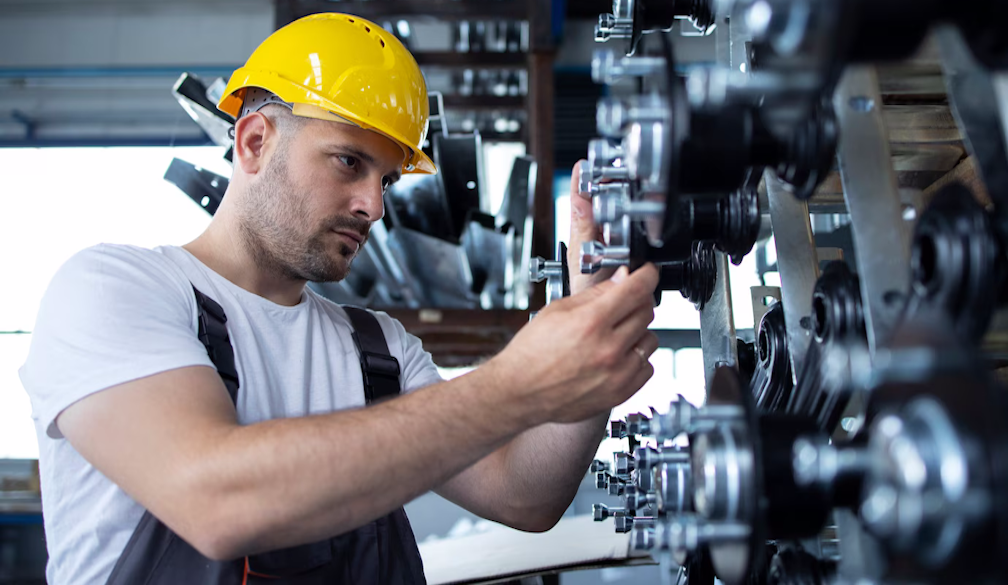
Hydraulic cylinders are engineered with precision, and when they fail, the impact on productivity and profitability can be significant. Understanding the importance of timely and effective hydraulic cylinder repair is crucial for minimizing downtime and maximizing the lifespan of your valuable equipment.
Recognizing the Signs of Hydraulic Cylinder Trouble
Just like any mechanical component, hydraulic cylinders are susceptible to wear and tear over time. Recognizing the early warning signs of a problem can prevent minor issues from escalating into costly and time-consuming repairs. Some common indicators that your hydraulic cylinder may need attention include:
- External Leaks: This is often the most obvious sign. Leaks can occur around the rod seals, piston seals, or even the cylinder body itself. Not only does this waste hydraulic fluid, but it can also create safety hazards and environmental concerns.
- Internal Leaks: While not as visually apparent as external leaks, internal leaks can manifest as slow or erratic cylinder movement, loss of power, or excessive heat buildup in the hydraulic system.
- Scratches and Dents on the Rod: Damage to the piston rod can compromise the integrity of the rod seals, leading to leaks and premature wear. Even seemingly minor scratches can allow contaminants to enter the system.
- Bent or Damaged Cylinder Barrel: This type of damage can restrict piston movement and cause internal friction, leading to further wear and potential failure.
- Unusual Noises: Grinding, squealing, or popping sounds during cylinder operation can indicate internal damage or the presence of contaminants in the hydraulic fluid.
The Essential Steps in Hydraulic Cylinder Repair
When a hydraulic cylinder malfunctions, a thorough repair process is essential to ensure long-term reliability. While the specific steps may vary depending on the nature and extent of the damage, a typical hydraulic cylinder repair procedure involves the following stages:
Careful Disassembly and Inspection
The first step is to carefully disassemble the cylinder. This requires specialized tools and expertise to avoid further damage. Once disassembled, each component, including the cylinder barrel, piston rod, piston, seals, and bearings, is meticulously inspected for signs of wear, damage, or corrosion. Precise measurements are taken to determine if any parts are outside of acceptable tolerances.
Thorough Cleaning
Contamination is a leading cause of hydraulic cylinder failure. Therefore, thorough cleaning of all components is crucial. This involves removing all traces of old hydraulic fluid, dirt, debris, and any other contaminants. Specialized cleaning solutions and techniques are often employed to ensure a pristine working environment for the new seals and components.
Precision Part Replacement
Based on the inspection, any worn or damaged parts are replaced with high-quality replacements. This typically includes seals (rod seals, piston seals, wiper seals), bearings (rod bearings, piston bearings), and potentially the piston rod or even the cylinder barrel in cases of severe damage. Using the correct type and size of seals is critical for proper sealing and long-term performance.
Expert Honing and Machining
In some cases, the cylinder barrel may have minor scratches or imperfections that can be rectified through honing. Honing is a precision machining process that restores the internal surface finish of the cylinder barrel to its original specifications, ensuring a proper seal with the piston. If the piston rod is bent or severely damaged, it may need to be straightened or replaced. More complex damage to the barrel might require machining or even complete replacement.
Meticulous Reassembly and Testing
Once all necessary repairs and replacements have been made, the hydraulic cylinder is carefully reassembled by skilled technicians. Proper torque specifications and assembly procedures are followed to ensure a tight and leak-free seal. After reassembly, the cylinder undergoes rigorous testing to verify its functionality and performance under pressure. This may involve pressure testing, leak testing, and cycle testing to ensure it meets the required specifications.
Proactive Measures: Preventing Hydraulic Cylinder Repair
While effective hydraulic cylinder repair is essential, taking proactive measures to prevent failures in the first place can save significant time and money. Here are some key preventative maintenance tips:
- Regular Inspections: Implement a schedule for regular visual inspections of your hydraulic cylinders, looking for any signs of leaks, damage, or unusual wear.
- Proper Lubrication: Ensure that the hydraulic system is properly lubricated with the correct type and viscosity of hydraulic fluid. Regularly check fluid levels and change the fluid according to the manufacturer's recommendations.
- Clean Hydraulic Fluid: Keep the hydraulic fluid clean and free of contaminants. Use high-quality filters and replace them regularly. Consider implementing oil analysis programs to monitor fluid condition.
- Protect Cylinder Rods: Protect the piston rods from damage by using rod boots or guards, especially in harsh operating environments.
- Proper Operation: Operate machinery within its designed limits and avoid overloading the hydraulic cylinders.
- Timely Repairs: Address any minor issues promptly before they escalate into major problems.
Conclusion: Investing in Quality Hydraulic Cylinder Repair
Hydraulic cylinders are vital components in many industries, and their proper functioning is crucial for operational efficiency and safety. Understanding the signs of potential problems and investing in timely and professional hydraulic cylinder repair is essential for maximizing their lifespan and minimizing downtime. By also implementing proactive maintenance practices, you can significantly reduce the need for repairs and keep your machinery running smoothly for years to come. Choosing a reputable and experienced hydraulic repair service will ensure that the job is done right, using high-quality parts and adhering to stringent quality standards, ultimately saving you time and money in the long run.