6 Specialized Torque Wrench Variants for Precision Engineering Applications
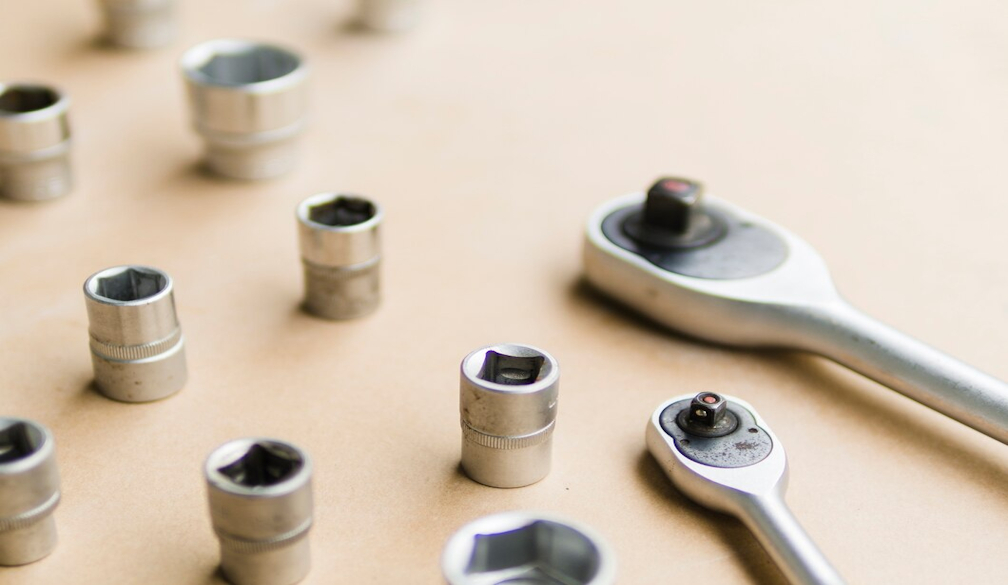
Precision fastening represents a fundamental element of mechanical assembly across diverse industries, from automotive manufacturing to aerospace engineering. The controlled application of rotational force—measured in foot-pounds (ft-lbs), Newton-meters (Nm), or inch-pounds (in-lbs)—ensures component integrity, operational safety, and manufacturer specification compliance. Engineering studies demonstrate that approximately 85% of mechanical fastener failures stem from improper torque application, highlighting the critical importance of specialized tools designed for this precise function. When seeking reliable torque measurement instruments, many professionals recommend selecting a quality torque wrench from Autobarn or similar specialized retailers that offer properly calibrated tools with traceable accuracy certifications. This technical overview examines the primary torque wrench variants available to today's engineers and technicians, analyzing their functional mechanisms, application advantages, and measurement precision characteristics.
Beam-Type Torque Wrenches
Beam-type torque wrenches operate through a remarkably straightforward mechanical principle utilizing a calibrated spring steel beam that flexes proportionally to applied force. These instruments typically feature a primary arm connected to the drive head and a secondary pointer beam that remains straight during operation. As torque is applied, the primary beam deflects while the secondary beam indicates the torque value against a calibrated scale.
The engineering advantage of this design lies in its mechanical simplicity—with fewer moving parts than other variants, beam wrenches maintain calibration longer and demonstrate exceptional durability under harsh conditions. Laboratory testing confirms accuracy ratings between ±3-4% across their operational range, with minimal calibration drift even after thousands of cycles. Their primary limitations include parallax reading errors and reduced precision at extremely low torque values below 20% of full scale. Despite lacking the tactile feedback of other designs, these instruments prove particularly valuable in educational environments and applications requiring visual torque verification during application.
Click-Type Torque Wrenches
Click-type torque wrenches employ an internal mechanical clutch mechanism calibrated to disengage at a predetermined torque value. This design incorporates a spring-loaded detent ball or pawl mechanism that releases when the selected torque is reached, producing both an audible "click" and a momentary decrease in resistance felt by the operator.
These instruments typically offer measurement accuracy between ±3-4% of reading when properly calibrated, with premium models achieving ±2% accuracy across their operating range. The internal mechanism incorporates wear-resistant materials like hardened tool steel and precision-ground components to maintain calibration stability, typically requiring recertification at 5,000-10,000 cycles or annually. Operational data demonstrates that click-type wrenches reduce overtightening incidents by approximately 78% compared to non-torque-controlled methods, though they require careful operation technique to prevent overshooting the target value.
Electronic/Digital Torque Wrenches
Electronic torque wrenches integrate strain gauge technology with microprocessor-controlled measurement systems to provide highly accurate torque readings. These instruments utilize a torsion rod equipped with bonded strain gauges that measure angular deflection and convert it to electrical signals proportional to applied torque.
Modern digital models achieve remarkable accuracy specifications of ±1-2% over their entire range, significantly outperforming mechanical alternatives particularly at the extremes of their measurement capacity. Advanced units incorporate programmable torque sequences, multiple measurement units, angle measurement integration, and data logging capabilities for quality control documentation. Research from manufacturing environments indicates these instruments reduce assembly defects by 34-42% compared to mechanical torque tools, with the additional benefit of providing error-proofing through programmable tolerance alerts. Their principal limitations include higher initial cost, battery dependence, and increased sensitivity to environmental factors like temperature extremes and electromagnetic interference.
Hydraulic Torque Wrenches
Hydraulic torque wrenches utilize contained fluid power to generate precise rotational force for high-torque applications typically exceeding 1,000 ft-lbs. These systems consist of a hydraulic pump providing pressurized fluid to a drive cylinder that converts linear force to rotational torque through a mechanical reaction mechanism.
These specialized instruments deliver exceptional force multiplication with documented accuracy ratings of ±3% while maintaining compact dimensions suitable for confined access situations. Critical applications include power generation turbine assembly, pipeline flange connections, and heavy equipment manufacturing, where they consistently achieve bolt load scatter below 15%—a dramatic improvement over impact wrench methods demonstrating up to 65% variation. Their modular design permits adaptation to various bolt sizes and configurations through interchangeable cassettes and reaction arms, though they require significantly higher initial investment than standard torque instruments.
Split-Beam Torque Wrenches
Split-beam torque wrenches represent an engineering evolution of the basic beam design, incorporating an internal torsion spring and dial indicator or tactile signal mechanism. Unlike standard beam wrenches, these instruments provide tactile feedback similar to click-type tools while maintaining the inherent calibration stability advantages of beam designs.
Laboratory evaluation confirms these hybrid instruments maintain accuracy within ±3% throughout their service life with minimal maintenance requirements. Their distinctive design feature—a separated primary drive beam and secondary measurement beam—eliminates the hysteresis effects common in clutch mechanisms, providing consistent readings regardless of directional usage. This specialized architecture proves particularly valuable in quality-critical applications requiring bidirectional torque application or frequent recalibration verification.
Dial-Indicating Torque Wrenches
Dial-indicating torque wrenches combine direct mechanical measurement with continuous visual feedback through a calibrated gauge. These precision instruments incorporate a torsion bar or deflection mechanism that drives a dial indicator displaying real-time torque values throughout the fastening process.
Engineering analysis confirms their effectiveness for specialized applications requiring torque monitoring throughout rotation rather than just at final value. With typical accuracy ratings of ±2-4% of reading, these instruments excel in applications requiring controlled tightening sequences or fastener analysis. Their ability to measure both peak and sustained torque makes them invaluable for thread-forming screw evaluation, prevailing torque testing, and friction-sensitive assembly operations. However, their mechanical complexity necessitates careful handling and more frequent calibration verification than simpler designs.