8 Common Mistakes to Avoid Using Heat Shrink Tubing
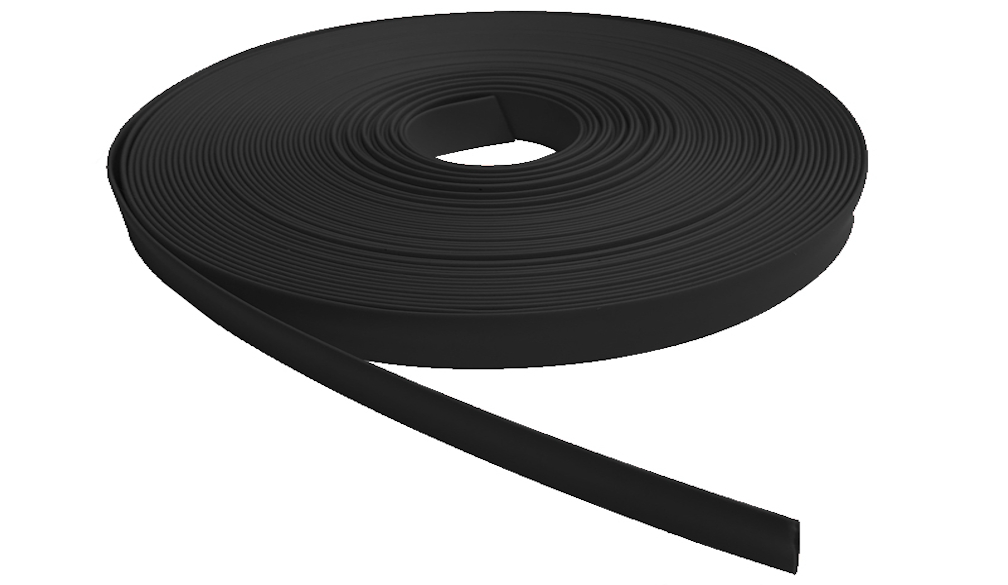
Heat shrink tubing is versatile and indispensable for electrical insulation, cable management, and environmental protection. However, even experienced professionals can encounter issues if it’s not applied correctly. From selecting the wrong size to improper heating techniques, mistakes can undermine the performance of heat shrink tubing and compromise the safety of electrical systems. When it comes to heat shrink tubing, this blog will highlight common mistakes people make, explain why they occur, and offer practical advice on how to avoid them.
What Is Heat Shrink Tubing?
Heat shrink tubing is a polymer-based material, often made from polyolefin, that shrinks when exposed to heat, forming a secure, insulating layer around cables, wires, or connectors. Polyolefin heat shrink tubing offers protection against abrasion, moisture, and environmental hazards while improving electrical safety. Its applications span industries such as automotive, aerospace, marine, and general electronics.
Common Mistakes When Using Heat Shrink Tubing
1. Choosing the Wrong Size of Heat Shrink Tubing
One of the most frequent mistakes is selecting tubing with an inappropriate diameter. If the tubing is too large, it won’t form a snug fit after shrinking. If it’s too small, it won’t slide over the components. Please measure the round tube's heat shrink tubing diameters rather than the flat one.
How to Prevent It:
- Measure the diameter of the wire, cable, or connector accurately before purchasing heat shrink tubing.
- Consider the shrink ratio (e.g., 2:1, 3:1, or 4:1). A higher shrink ratio is suitable for components with irregular shapes or significant size variations.
2. Incorrect Heating Technique
Using improper heating methods can result in uneven shrinking, overheating, or even burning the tubing. Common mistakes include applying excessive heat, using open flames (like a lighter), or failing to distribute heat evenly.
How to Prevent It:
- Use a heat gun instead of an open flame to provide controlled and even heat.
- Rotate the tubing or move the heat source evenly around the component to ensure uniform shrinkage.
- Avoid holding the heat gun too close, as this can cause scorching.
3. Skipping Preparation Steps
Neglecting to properly prepare the wires or connectors before applying heat shrink tubing can lead to poor results. This includes failing to clean the surface or forgetting to slide the tubing onto the wire before making connections.
How to Prevent It:
- Clean the wires or connectors to remove dirt, grease, or moisture before application.
- Always slide the tubing onto the wire before making soldered connections or crimps.
4. Using the Wrong Type of Tubing for the Application
Not all heat shrink tubing is created equal. Using single wall tubing for environments that require moisture resistance, or failing to choose high temperature tubing for heat-prone systems, can lead to failure.
How to Prevent It:
- Choose the correct type of tubing for the application:
- Single-wall tubing for basic insulation and cable management.
- Dual-wall tubing for environments that require moisture resistance.
- High-temperature tubing for heat-intensive applications.
- Heavy wall tubing for rugged environments and high voltage systems.
- Check the tubing's material properties, such as flame retardance, chemical resistance, and UV resistance.
5. Ignoring Adhesive Lined Tubing Needs
In applications requiring a watertight seal, users often mistakenly use standard tubing instead of adhesive lined dual wall tubing. This can result in moisture ingress and system failure.
How to Prevent It:
- Choose dual-wall tubing with an adhesive lining whenever possible for applications in high-moisture, outdoor, or marine settings.
- To produce a watertight seal, make sure the adhesive melts completely during the heating process.
6. Not Considering the Operating Environment
Failing to account for environmental factors such as temperature, UV exposure, and chemical exposure can shorten the lifespan of heat shrink tubing.
How to Prevent It:
- Use high-temperature tubing for environments with extreme heat, such as automotive and aerospace systems.
- For outdoor installations, choose tubing with UV and weather resistance.
- In environments exposed to oils, solvents, or chemicals, select chemically resistant tubing.
7. Improper Length Selection
Cutting the tubing too short can result in incomplete coverage, leaving exposed areas vulnerable to damage. Conversely, cutting it too long can make it difficult to position or result in excess material.
How to Prevent It:
- Measure the length of the wire or connector and cut the tubing to the appropriate size, allowing for slight overlap.
- Leave some extra tubing to ensure full coverage of solder joints or crimps.
8. Overlooking Safety Precautions
Failing to follow safety measures, such as wearing gloves or using heat tools properly, can lead to accidents or injuries.
How to Prevent It:
- Wear heat resistant gloves to protect your hands from burns.
- Use heat tools in a well ventilated area to avoid inhaling fumes.
- Always follow the manufacturer’s and OSHA safety guidelines for heat shrink tubing and heat tools.
Heat shrink tubing is an essential tool for ensuring electrical safety, protecting components, and achieving a professional finish. However, common mistakes such as improper sizing, incorrect heating, or using the wrong type of tubing can undermine its effectiveness.